Filter Technology Offers
Featured
Category
Topic
- Electronics, IT and Telecomms
- Industrial manufacturing, Material and Transport Technologies
- Industrial Technologies
- Energy Technology
- Energy Storage and Transport
- Energy production, transmission and conversion
- Fossil Energy Sources
- Nuclear Fission / Nuclear Fusion
- Renewable Sources of Energy
- Rational use of energy
- Other Energy Topics
- Energy efficiency
- Carbon capture and energy
- Biogas and anerobic digestion (AD)
- Physical Sciences and Exact Sciences
- Biological Sciences
- Agriculture and Marine Resources
- Agrofood Industry
- Measurements and Standards
- Protecting Man and Environment
- Social and Economics concerns
- Lightweight
- Sustainability
- Digitalization
- Opthalmology
- Aerospace
- Communications
- Computer related
- Electronics Related Market
- Genetic Engineering / Molecular Biology
- Medical Health related
- Energy Market
- Consumer related
- Industrial Products
- Other
Country
Showing all visible results for Energy Technology
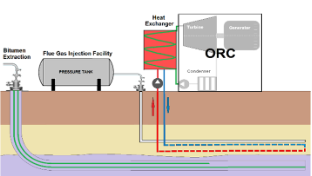
Patents for licensing
- +1 day
- Hide post
Equitus Design Engineering and Innovations Limited
0 followers
4 publications
Equitus Design Engineering and Innovations Limited posted this:
0 followers
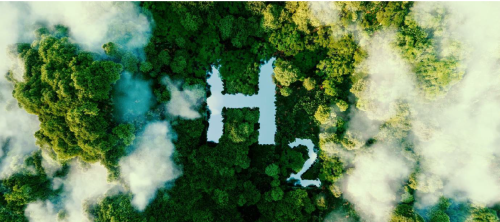
Complete End to End Solar Green Hydrogen Solution Including Production, Storage and Applications
Innovative Products and Technologies
- +2 weeks
- Hide post
Dirección de Transferencia Tecnológica (DIT) Contact: Martín Flores Donoso
3 followers
10 publications
Dirección de Transferencia Tecnológica (DIT) Contact: Martín Flores Donoso posted this:
3 followers
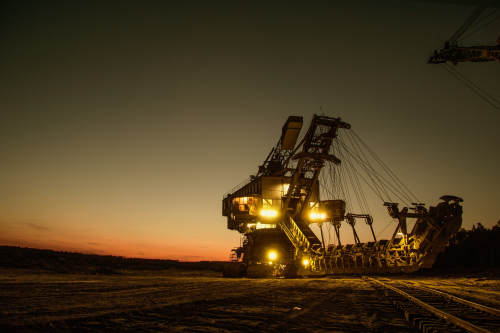
Smart Fortification Kit for mining and building work sites
Knowhow and Research output
- +3 weeks
- Hide post
University of Alberta, Technology Transfer Services
2 followers
34 publications
University of Alberta, Technology Transfer Services posted this:
2 followers
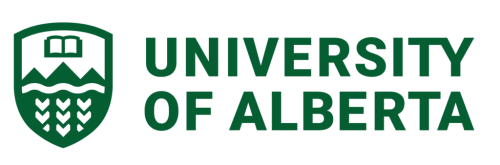
Methods of Efficient Lignin Conversion
Innovative Products and Technologies
- +3 weeks
- Hide post
Dirección de Transferencia Tecnológica (DIT) Contact: Martín Flores Donoso
3 followers
10 publications
Dirección de Transferencia Tecnológica (DIT) Contact: Martín Flores Donoso posted this:
3 followers
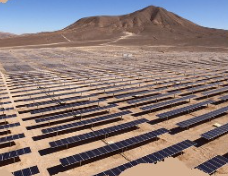
GEMA (Energy Micro-web Storage Managerial)
Knowhow and Research output
- +1 month
- Hide post
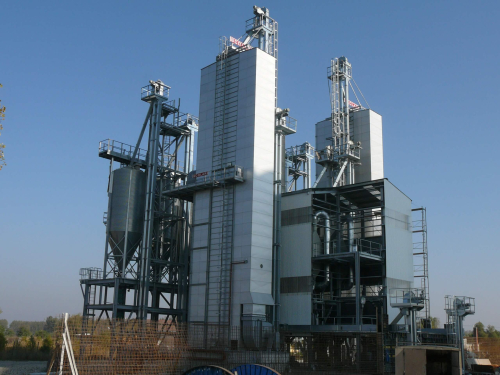
Grain dryer with low fuel consumption and environmentallyf friendly.
Innovative Products and Technologies
- +2 months
- Hide post
Universidad de Alicante
25 followers
119 publications
Universidad de Alicante posted this:
25 followers
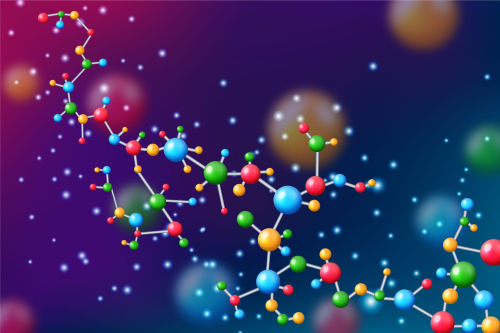
Transformation of biomass waste to obtain catalysts of interest to the chemical industry
Patents for licensing
- +2 months
- Hide post
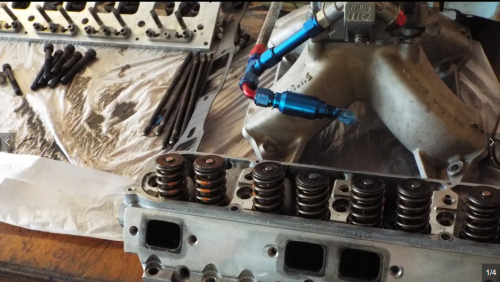
Variable Lift Valve Train Technology for Reduced Emissions and Improved Engine Performance
Patents for licensing
- +2 months
- Hide post
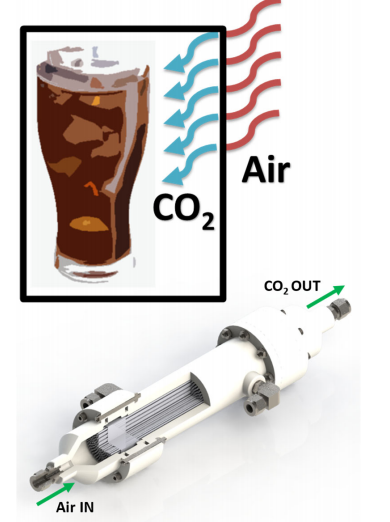
Carbonator - Small Scale Beverage Carbonation on Demand
Investment Opportunities in Startups and Spinoffs
- +5 months
- Hide post
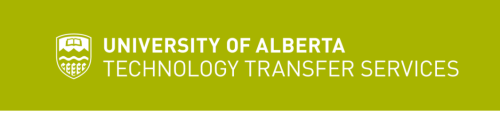
Methods of Catalysis for Enhanced Methanol Production from Carbon Dioxide (CO2)
Innovative Products and Technologies
- +5 months
- Hide post

Sustainable concrete with recycled concrete aggregate and wind turbine blade waste
Patents for licensing
- +5 months
- Hide post