Showing 1 to 15 of 372 results

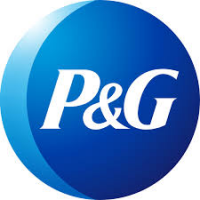
Seeking Rapid Substance Detection in Inspection and Supply Chain
Specific Technical Innovation The Procter & Gamble Company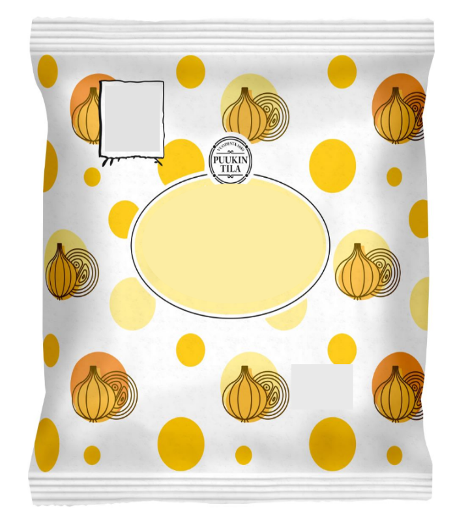
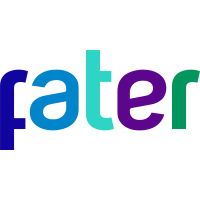
Seeking Glue-free and Plastic-free closure of paper packaging
Specific Technical Innovation Fater SpA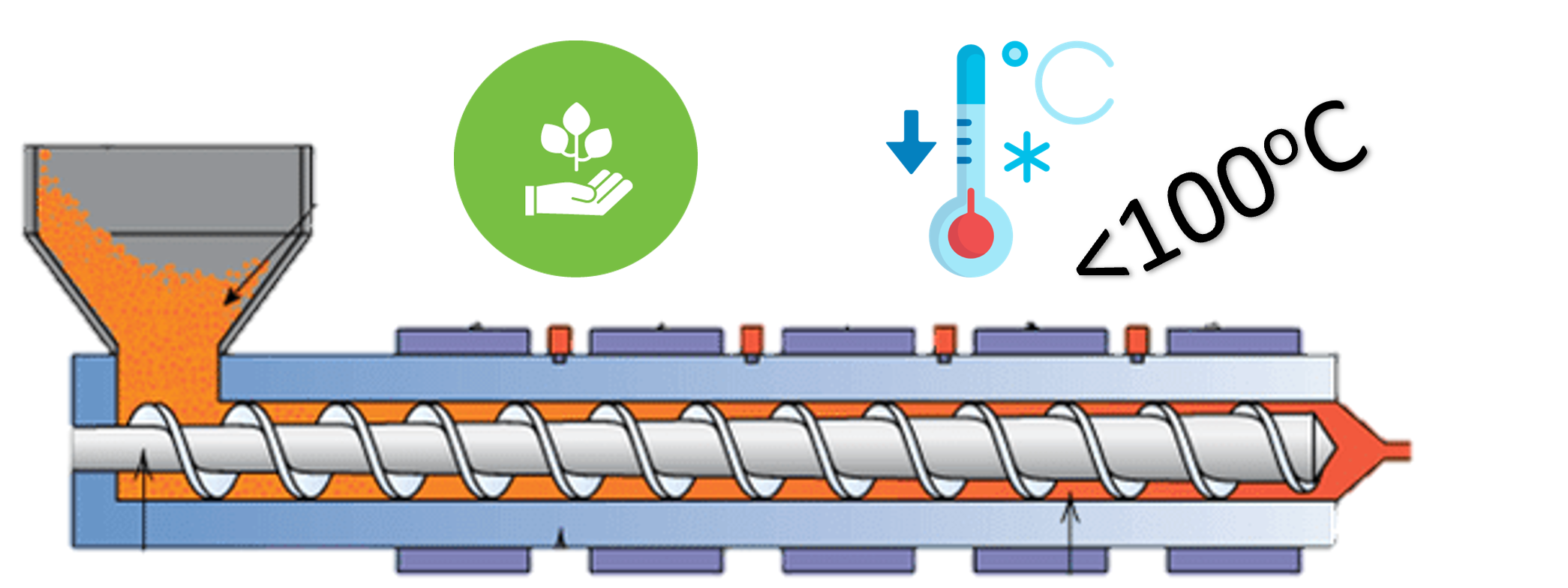

Seeking Sustainable Bio-Based Material for Low-Temperature Extrusion in FMCGs/CPGs
Specific Technical Innovation Organization from European Union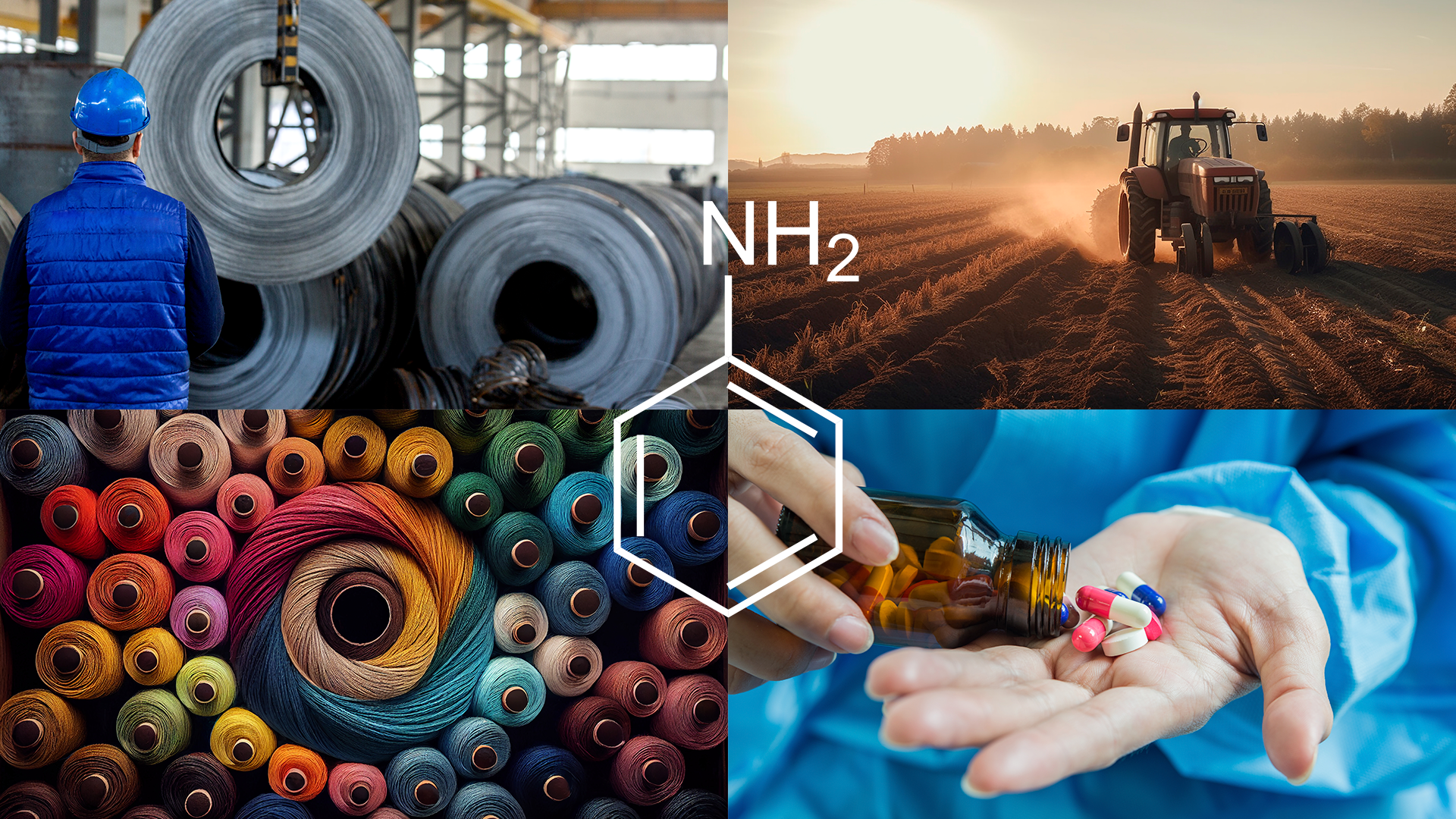
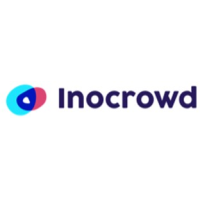
Seeking Diversifying Business Models for Aniline and Derivatives
Specific Technical Innovation inocrowd![Seeking Revolutionizing Process Efficiency and Effectiveness through Digital Technologies in Technologies in Chemical Production P[…]](https://static3.innoget.com/uploads//3382d57665093802723a79f0d5d53a0276dc8f04.jpg)
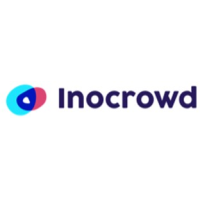
Seeking Revolutionizing Process Efficiency and Effectiveness through Digital Technologies in Technologies in Chemical Production P[…]
Specific Technical Innovation inocrowd![Seeking Sustainable packaging: Development of barrier properties to oil and grease in molded fiber (cellulose) articles (MFA) for […]](https://static5.innoget.com/uploads//4f43b4f7ede6d0b7a75de93d2d3380d7572f311e.jpg)
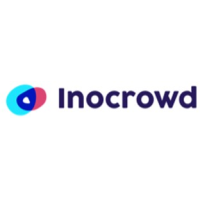
Seeking Sustainable packaging: Development of barrier properties to oil and grease in molded fiber (cellulose) articles (MFA) for […]
Specific Technical Innovation inocrowd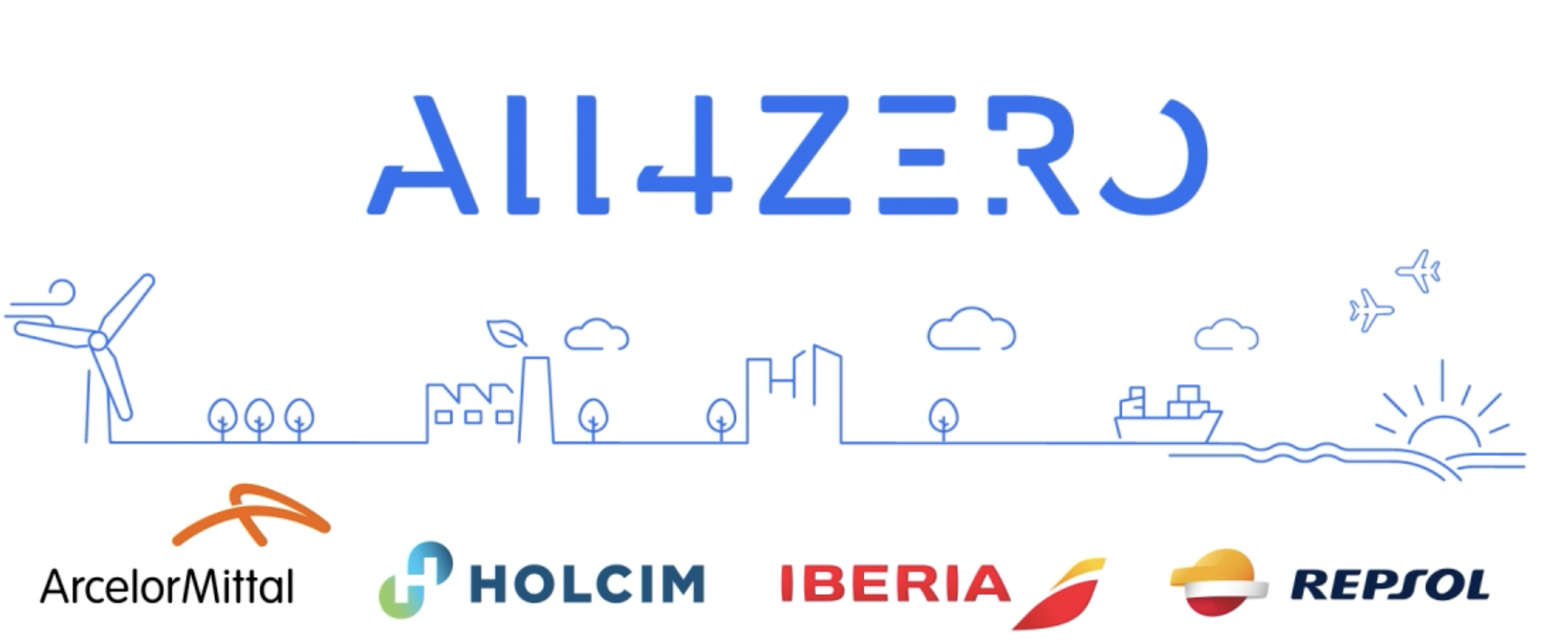
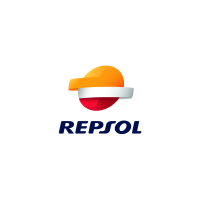
Seeking: How can we reduce costs and increase efficiency when obtaining renewable hydrogen
Specific Technical Innovation Repsol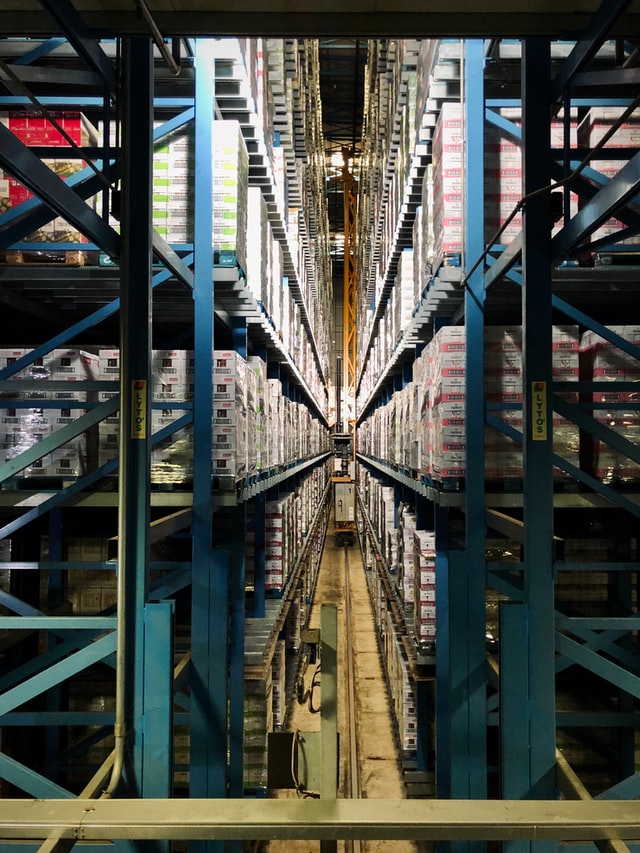
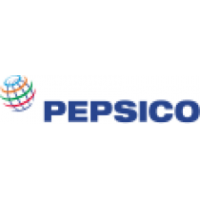
Seeking technologies to reduce GHGs in all aspects of the supply chain and manufacturing process.
Specific Technical Innovation PepsiCo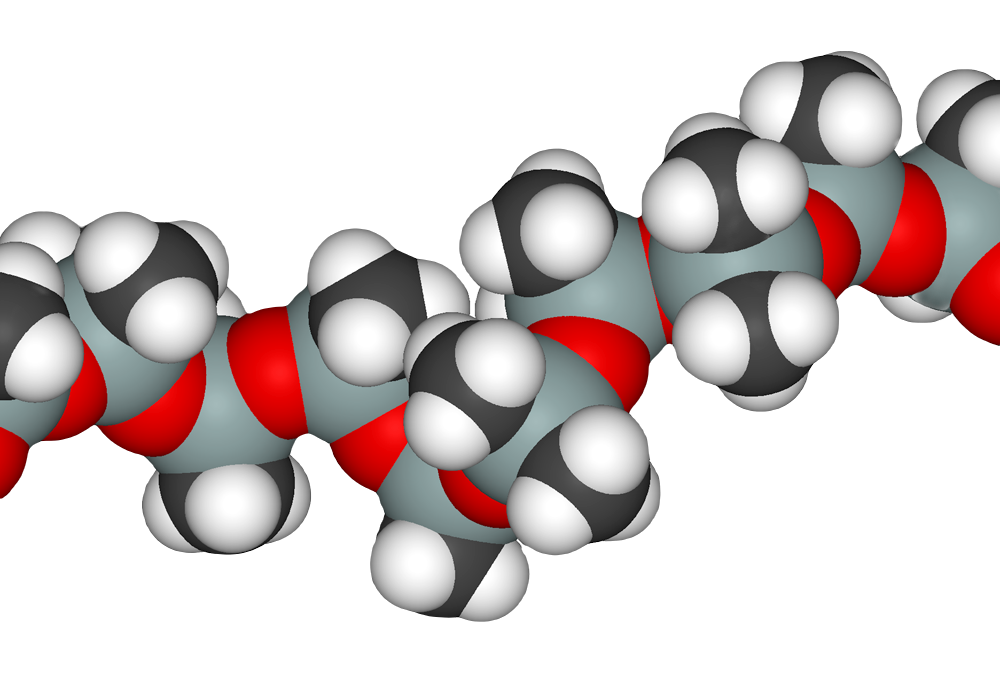

Seeking Adhesion improvement of silicone-based coatings to metal substrate
Specific Technical Innovation Organization from European Union

Seeking PFAS-free Low-Friction Coating for metallic cutting edges
Specific Technical Innovation Organization from European Union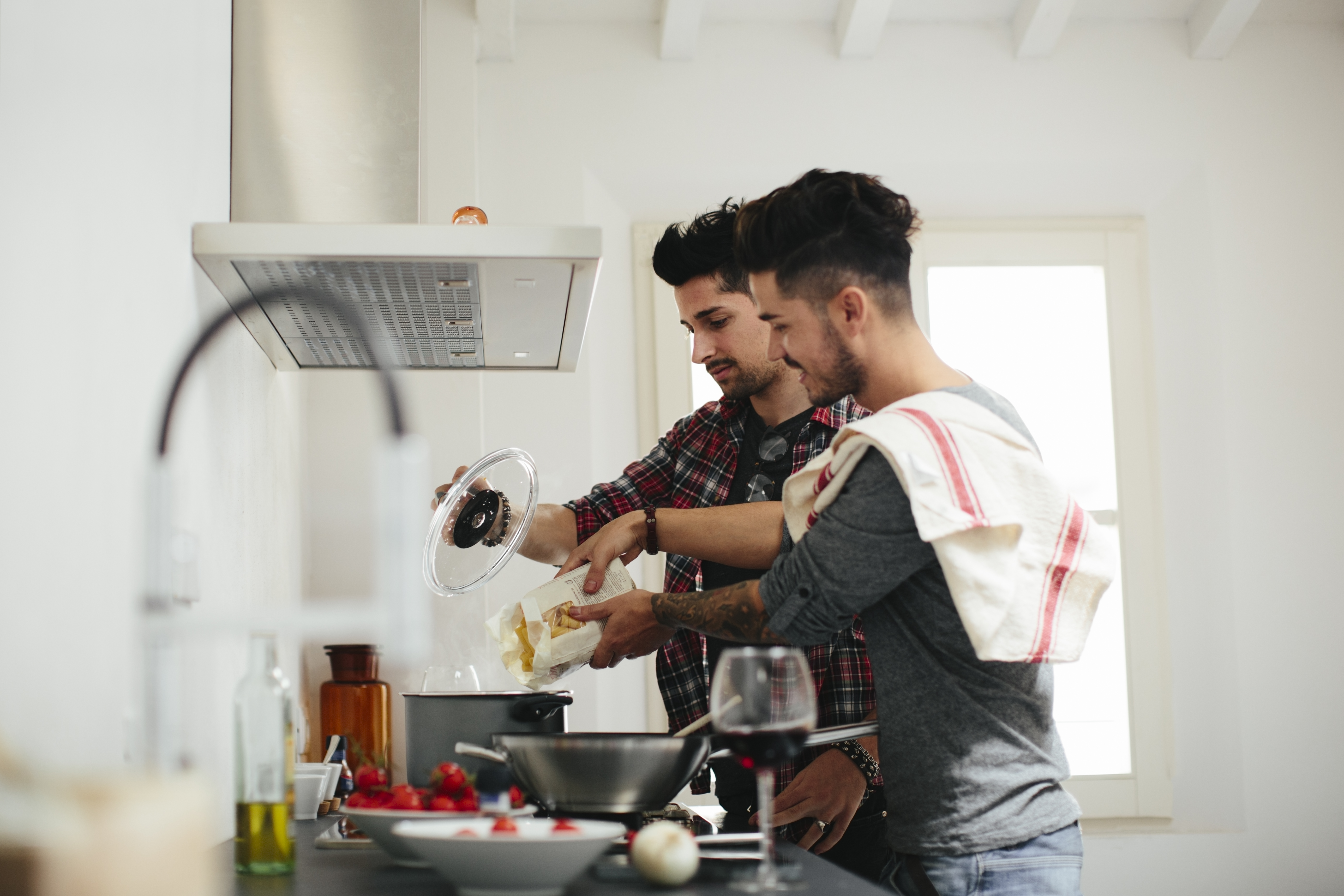
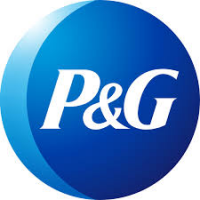
Seeking existing market solutions targeted towards crawling insects
Ready to Market Technical Innovations and Products The Procter & Gamble Company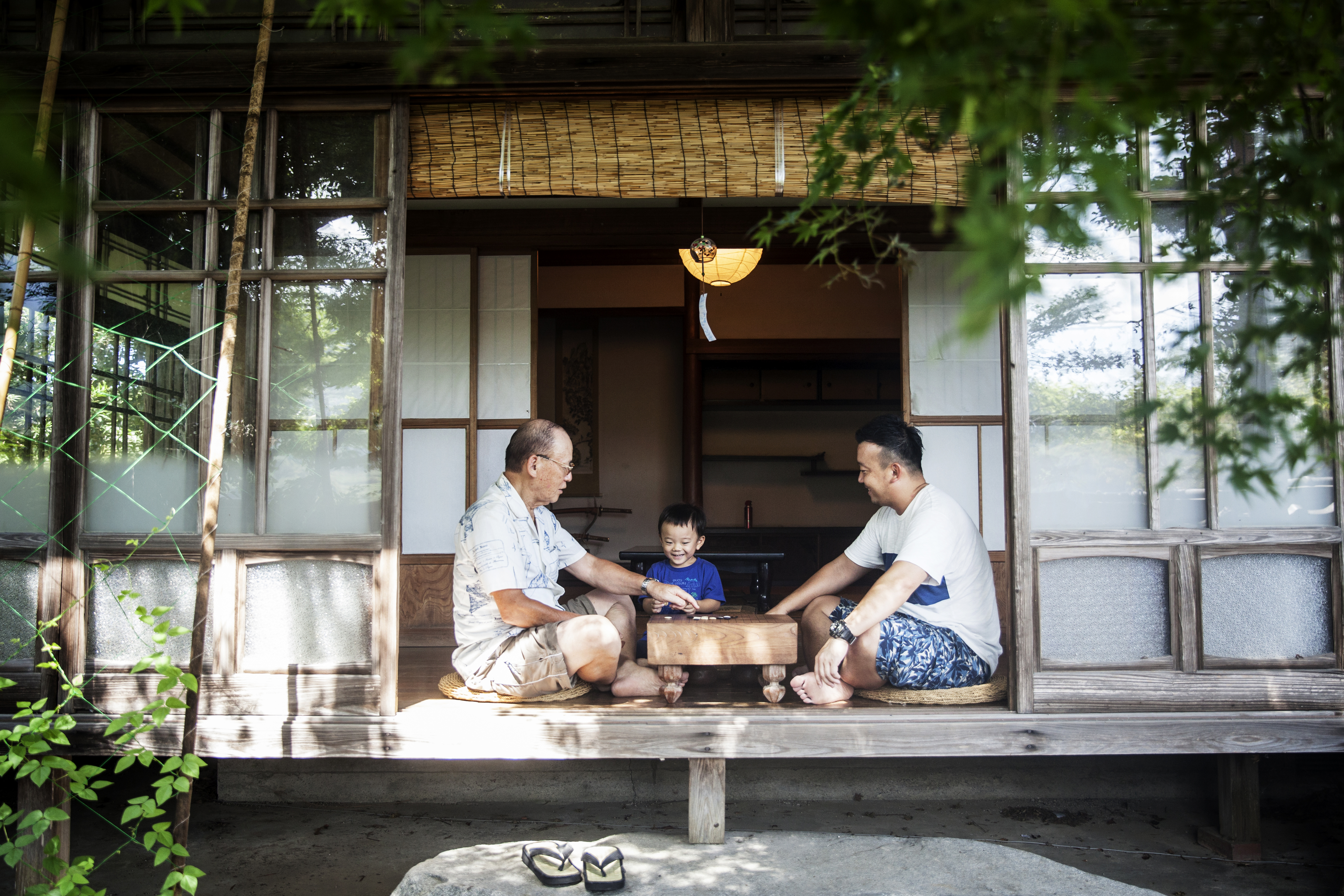
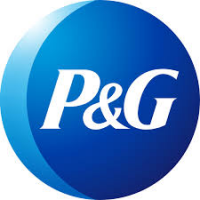
Seeking safe and effective outdoor mosquito solutions
Ready to Market Technical Innovations and Products The Procter & Gamble Company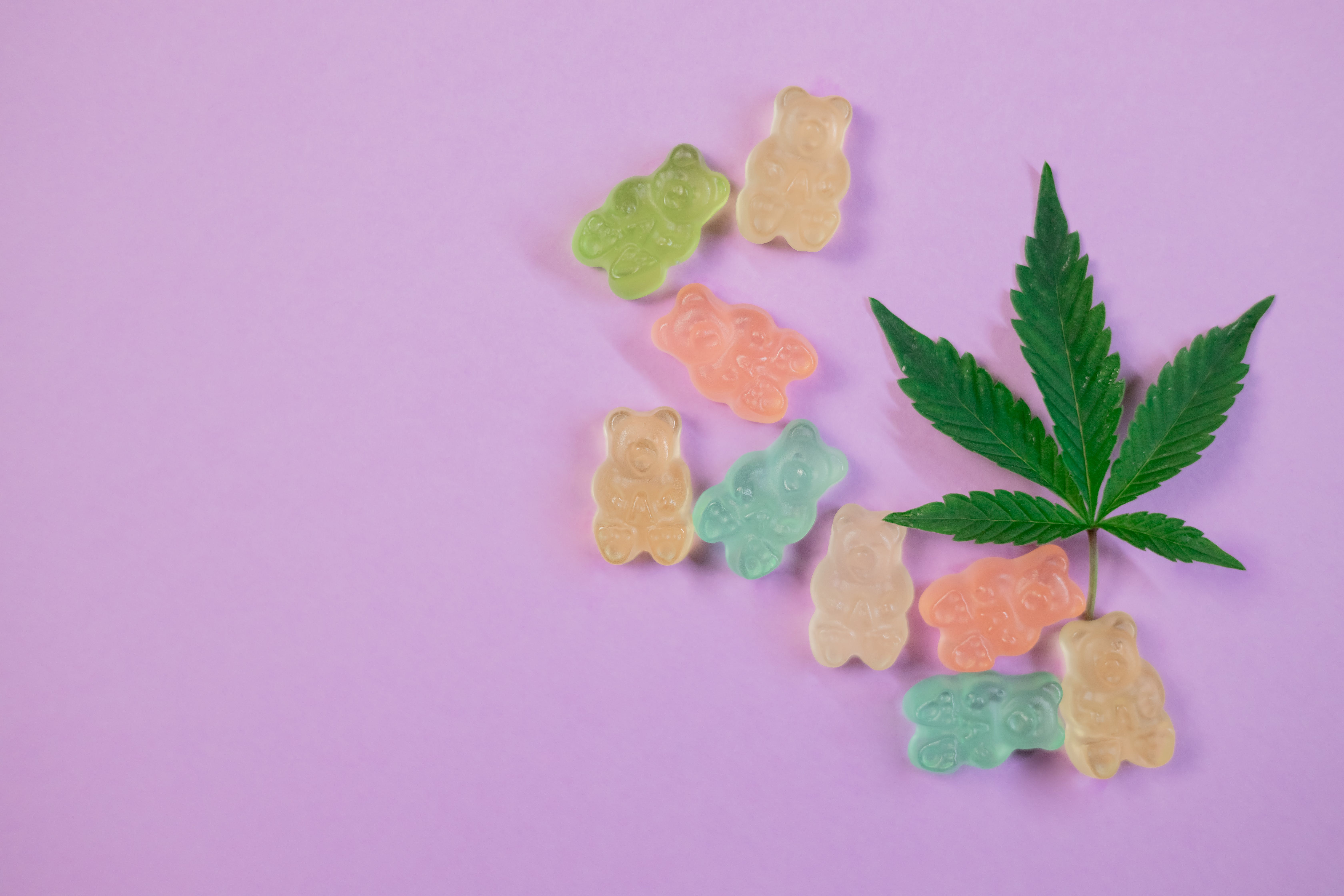
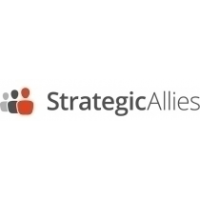
Seeking technologies & expertise to improve the bioavailability of cannabinoids
Ready to Market Technical Innovations and Products Strategic Allies Ltd.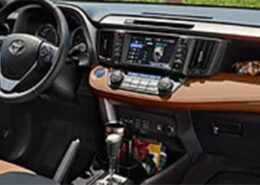
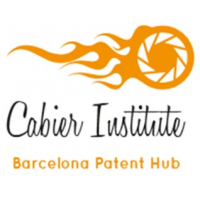
Seeking patents for license: DE, EP and US issued patents
Specific Technical Innovation CABIER INSTITUTE, SL
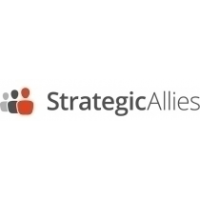